Quality Management System: ISO 9001:2015
If you’re looking for expert guidance, HSEPro’s ISO 9001 consultants in UAE offer comprehensive support for businesses across all sectors. As one of the best ISO 9001 consultancy companies in Dubai, we specialize in ISO 9001 implementation, documentation support, internal audit services, and ISO 9001 compliance consultancy tailored to your business needs.
Our team provides end-to-end ISO 9001 consultancy services in UAE, including QMS setup, gap analysis, internal auditor training, and audit preparation services—all designed to help you meet ISO 9001 requirements confidently.
A robust ISO 9001 quality management system (QMS) includes your organization’s structure, planning, documented information, and operational processes used to meet customer and stakeholder expectations. Whether you’re a construction company, manufacturing unit, trading business, service provider, or part of the logistics industry, we help you enhance your operations, reduce risk, and ensure long-term compliance.
Our ISO experts also help organizations that need ISO 9001 compliance urgently by providing fast-track consulting, document preparation, and full audit readiness within tight timelines. If you’ve been searching for a local ISO 9001 expert in UAE, or wondering “Who can help me get ISO 9001 certified?” — HSEPro is your answer.
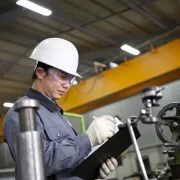
To know the comprehensive overview of the Quality Management System, click the button below.
What is ISO 9001?
ISO: Quick Guide to ISO 9001:2015 Quality Management Systems
What are the benefits in implementing ISO 9001?
An ISO 9001:2015 Quality Management System needs to be established, implemented, maintained, and continually improved—including the processes needed and their interactions—based on the provisions of the standard. For organizations wondering how to get ISO 9001 certified or seeking help from an ISO 9001 consultant near me, the advantages are significant.
Key potential benefits include:
Provides a systematic approach to fulfilling your organization’s objectives, enabling effective ISO 9001 implementation for small businesses and large enterprises alike, and driving consistent improvement in products and services.
Offers ISO 9001 documentation support that gives assurance to customers that the products or services will meet their requirements and specifications.
Enhances organizational performance while ensuring smooth audits through ISO 9001 internal audit services and expert ISO 9001 compliance consultancy.
Lays the foundation for sustainable development and long-term success with a proper quality management system setup in UAE.
If you’re navigating the ISO 9001 certification process step by step, our expert ISO 9001 services in UAE can guide you at every stage.
How to implement ISO 9001?
Few tips to get you started in implementing ISO 9001:
Analyze your company’s context that is relevant to Quality like the internal and external factors as well as the interested parties that might impact your business.
Decide the scope of the QMS, if what are your system boundaries.
Set your Quality policy and objectives.
Give the time frame if when you will implement the system and plan how to achieve it.
Identify any competence and resources gaps that need to be addressed before implementing the standard.
Consider to get support from any Consultant to speed-up the development and implementation of the Quality Management System.
Hiring a Consultant?
A consultant can guide you through the process of implementing, improving, and maintaining your Quality Management System (QMS). With the active participation of your team, this fosters a sense of ownership and reinforces the idea that your organization is responsible for its own QMS. Whether you’re looking to improve QMS for ISO 9001 or need help after a failed ISO 9001 audit, professional consultancy makes a difference.
An expert ISO 9001 consultant in Dubai or Abu Dhabi could assist in:
Preliminary status survey or assessment
Training
Implementation
Internal audits (ISO 9001 audit preparation services)
Choosing the right partner is essential. Select the best ISO 9001 consultancy company in Dubai by evaluating credentials, qualifications, and experience with your industry — whether you’re in construction, manufacturing, services, logistics, or trading.
If you need ISO 9001 compliance urgently, need to fix ISO 9001 non-conformities, or simply need help with ISO 9001 documentation, HSEPro Consultants is here to help. We provide trusted ISO 9001 consultancy in Abu Dhabi and across the UAE to help you get certified with confidence.
Email: consultancy@hsepro.org
Any organization that wants to improve its quality management system, meet customer and applicable statutory and regulatory requirements, and enhance customer satisfaction can use the ISO 9001 standard. It is suitable for organizations of any size, and applies to all sectors, including manufacturing, services, healthcare, education, government, and non-profit organizations. ISO 9001 can also be used by certification bodies or other third parties to assess an organization’s conformity with this International Standard.
ISO has a range of standards for quality management systems that are based on ISO 9001 and adapted to specific sectors and industries. These include:
The ISO 9001 standard specifies requirements for the establishment, maintenance, and continuous improvement of a quality management system, covering a wide range of topics including:
- Context of the organization: ISO 9001 requires organizations to determine the external and internal factors that affect their ability to achieve the intended results of their quality management system.
- Leadership: The standard emphasizes the importance of leadership in implementing and maintaining a quality management system.
- Planning: The quality management system must include measures designed to achieve an organization’s quality objectives and continuously improve the system’s effectiveness.
- Support: ISO 9001 addresses issues such as resources, competence, awareness, communication and documented information.
- Operation: The processes necessary to meet customer requirements and increase customer satisfaction must be planned, implemented and controlled.
- Performance evaluation: The standard requires organizations to monitor, measure, analyze and evaluate the performance and effectiveness of their quality management system.
- Improvement: ISO 9001 emphasizes the importance of continuously increasing the effectiveness of the quality management system based on the results of performance evaluation and other data sources.
Overall, ISO 9001 helps organizations address all aspects of managing the quality of their products and services, with an emphasis on customer satisfaction and constant enhancement of the quality management system.
The most recent revision of ISO 9001 was finalized in 2015. Ensuring that all ISO standards remain current and relevant for the marketplace is crucial. After extensive international consultation, a consensus was reached in August 2023 that revising the standard would add value. This revision aims to align ISO 9001 with the current needs of standard users and the communities they serve.
The revised version of ISO 9001 is expected to be published at the end of 2025.
The publication of the revised standard will present an excellent opportunity for you to review and update your quality management system. Take this chance to ensure that your system effectively addresses any changes and aligns well with your needs, as well as those of your customers and other stakeholders. At the time of publication, ample information will be provided about the updates made and how they may impact organizations.
In terms of validity of their certificates, organizations certified to ISO 9001:2015 will be granted a transition period to migrate their quality management system to the new edition of the standard.
Certification to ISO 9001 is one way to demonstrate to stakeholders and customers that you are committed and able to consistently deliver high quality products or services. Holding a certificate issued by an accredited conformity assessment body may bring an additional layer of confidence, as an accreditation body has provided independent confirmation of the certification body’s competence.
As with other ISO management system standards, companies implementing ISO 9001 can choose whether they want to go through a certification process or not.
Checking that the system works is a vital part of ISO 9001. The standard recommends that an organization performs internal audits to check how its quality management system is working. An organization may decide to invite an independent certification body to verify that it is in conformity with the standard, but there is no requirement for this. Alternatively, you might invite your clients to audit the quality system for themselves.
As in other contexts, standards should always be referred to with their full reference in statements on certification such as “certified to ISO 9001:2015” (not just: “certified to ISO 9001). If you wish to use a logo to demonstrate certification, please contact the certification body that issued your certificate. See full details about use of the ISO logo.
Support on auditing quality management systems can be found on the website of the ISO 9001 Auditing Practices Group. This is an informal group of quality management system experts, auditors and practitioners from ISO/TC 176 and the International Accreditation Forum.
A definition of quality is part of the core vocabulary for quality management which can be found in ISO 9000:2015 and applies to all ISO quality management standards, including ISO 9001. It says that quality is the “degree to which a set of inherent characteristics [or distinguishing features] of an object”, which in turn is defined as anything perceivable or conceivable, such as a product, service, process, person, organization, system or resource, “fulfils requirements.”
ISO 9001 and ISO 14001 are both International Standards for organizational management but they have different goals. ISO 9001 helps organizations improve their quality management and customer satisfaction. ISO 14001 helps organizations reduce their environmental impact and promote sustainability. ISO standards that look at different types of management systems, such as ISO 9001 for quality and ISO 14001 for environmental management, are all structured in the same way. This means that companies using one ISO management standard will find it easy to integrate other aspects of organizational management into their existing management system.
The International Standards ISO 9001 and ISO 13485 both define requirements for quality management systems, but one has a much broader user group than the other. ISO 9001 provides a quality management framework that can apply to organizations of any size or sector. ISO 13485, on the other hand, has been developed specifically for the medical device industry with a focus on regulatory compliance. The standard helps ensure the safety and effectiveness of medical devices, including risk management, traceability and process validation. Compared to ISO 9001, it contains additional requirements specific to organizations involved in the life cycle of medical devices, whereas elements of ISO 9001 that are not relevant as regulatory requirements are not part of ISO 13485.
In short, while ISO 9001 sets out a general framework for quality management, ISO 13485 provides specific guidance for the medical device industry.
For more information, visit: www.iso.org/standard/62085.html